Condition Monitoriningin Supply Chains
DHL Innovation Center, Bonn
and Univerisity of Siegen
5 mins read
Note
This is an excerpt from my 125 page master thesis, and it can not be fully shared due to the confidentiality agreement with the Deutsche Post DHL Group (now DHL group).
Motivation
The objective of this thesis is to address the critical challenge of maintaining product quality and stock levels in warehouses through effective condition monitoring based on the Internet of Things (IoT). The interaction between users and stakeholders via the IoT system is paramount for making timely and impactful decisions regarding inventory management. Perishable goods, such as those found in blood banks, food industries, chemicals, and pharmaceuticals, are particularly challenging to manage due to their sensitivity to environmental conditions and demand variability. Current regulations, such as the General Food Law, emphasize the need for transparency and traceability in product handling to mitigate quality issues and facilitate efficient recalls.
Existing traceability strategies often focus more on compliance and assurance systems than on real-time monitoring and proactive measures. For instance, vaccines require strict cold chain logistics to maintain efficacy, necessitating precise temperature control and immediate response to any deviations. Despite the availability of digital monitoring tools, the gap lies in ensuring that alerts are communicated effectively and acted upon promptly by warehouse personnel. Manual monitoring systems introduce risks of delayed response and lack of visibility into temperature discrepancies. Automated systems offer a solution by providing real-time alerts, yet the effectiveness of these systems hinges on the prompt and clear communication of these alerts to the relevant stakeholders.
This thesis aims to explore and propose enhancements in the interaction mechanisms within IoT-based monitoring systems to improve decision-making processes and ensure the integrity of sensitive products in storage.
Real world examples
Quality of products, if mishandled, could lead to severe damages at the end of the supply chain, the technological challenge in bringing teams together and to increase visibility about the storage process were the challenges faced.
Japan disposes 7,000 mishandled doses of COVID-19 vaccine
A hospital and a mass vaccination each had to dispose of some 1,000 doses of the Pfizer Inc. vaccine because they expired at room temperature, while 12 doses went to waste at a ward in Tokyo because of over-dilution, a survey by the daily found.
This image illustrates the impact of an accident or disruption on a business indicator over time, showing a decline from a stable situation into a dip during the disruption period. Eventually, the indicator recovers and reaches a new stable situation, highlighting the system's ability to adapt or recover.
-
Citation
- Monteleone, S., Sampaio, M. and Maia, R. F. (2017) “A novel deployment of smart Cold Chain system using 2G-RFID-Sys temperature monitoring in medicine Cold Chain based on Internet of Things,” Proceedings - 2017 IEEE International Conference on Service Operations and Logistics, and Informatics, SOLI 2017, 2017-Janua, pp. 205–210. doi: 10.1109/SOLI.2017.8120995.
Methodology
In partnership with the biggest third party logisitics company in the world – Deutsche Post DHL Group which delivers and handles senstive parcels in over 220 countries and territories worldwide.
Design Framework
The research is carried out under the Design Case Study framework (Wulf et al., 2015) to derive theories that help analyze work practices and information technology systems. The framework consists of three phases: Empirical Pre-Study, Prototyping/(Participating) IT Design, and Evaluation/Appropriation Study.
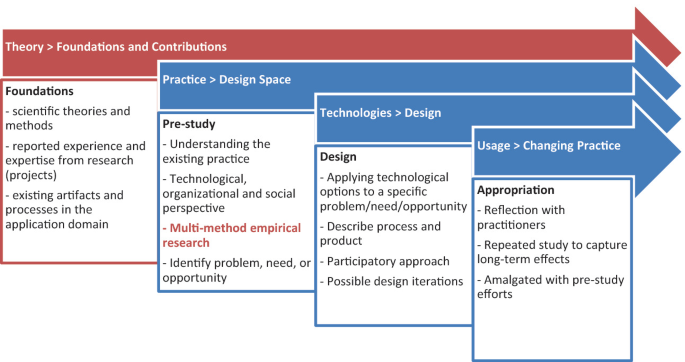
Focus: Due to the limited time available for the research, the thesis focuses on the first phase of the Design Case Study framework – Empirircal Pre-Study.
-
Citation
- Wulf, Volker & Rohde, Markus & Pipek, Volkmar & Stevens, Gunnar. (2011). Engaging with practices: Design case studies as a research framework in CSCW. Proceedings of the ACM Conference on Computer Supported Cooperative Work, CSCW. 505-512. 10.1145/1958824.1958902.
Recruitment of Participants
Scheduled visits and online interviews with DHL warehouses across 5 countries in Europe. Contact participants who met the following conditions: Participants with experience in condition monitoring of goods, participants with managerial experience inside a warehouse and participants that work with IoT systems for condition monitoring.
Participant Roles
Participant (Pseudonym) | Role |
---|---|
W | Site and Operation Manager |
X | Dangerous Goods Expert |
Y | Process Improvement, Quality Assurance Lead |
Z | IoT Product Design and Development Manager |
Data Collection + Data Analysis
- Grounded Theory approach by visiting and monitoring warehouses
- Semi-structured qualitative interviews via Zoom Cloud Meetings of 120 mins with participants.
- The flow for the interview guide is made as to the following, in no particular order: Personal information, Work Practices, Storage, Actors involved, The system used for monitoring, IoT’s role in the system, Interaction on the system, Collaboration via the system, Interaction Challenges
- User interviews were transcribed
- Thematic Analysis (a detailed 6 step process mentioned by Braun, V. & Clarke, V. (2012)) was done of the notes + transcripts + media content using MAXQDA
- Codes and Themes were developed
-
Citation
- Braun, V. & Clarke, V. (2012) Thematic analysis. In H. Cooper, P. M. Camic, D. L. Long, A. T. Panter, D. Rindskopf, & K. J. Sher (Eds), APA handbook of research methods in psychology, Vol. 2: Research designs: Quantitative, qualitative, neuropsychological, and biological (pp. 57-71). Washington, DC: American Psychological Association.
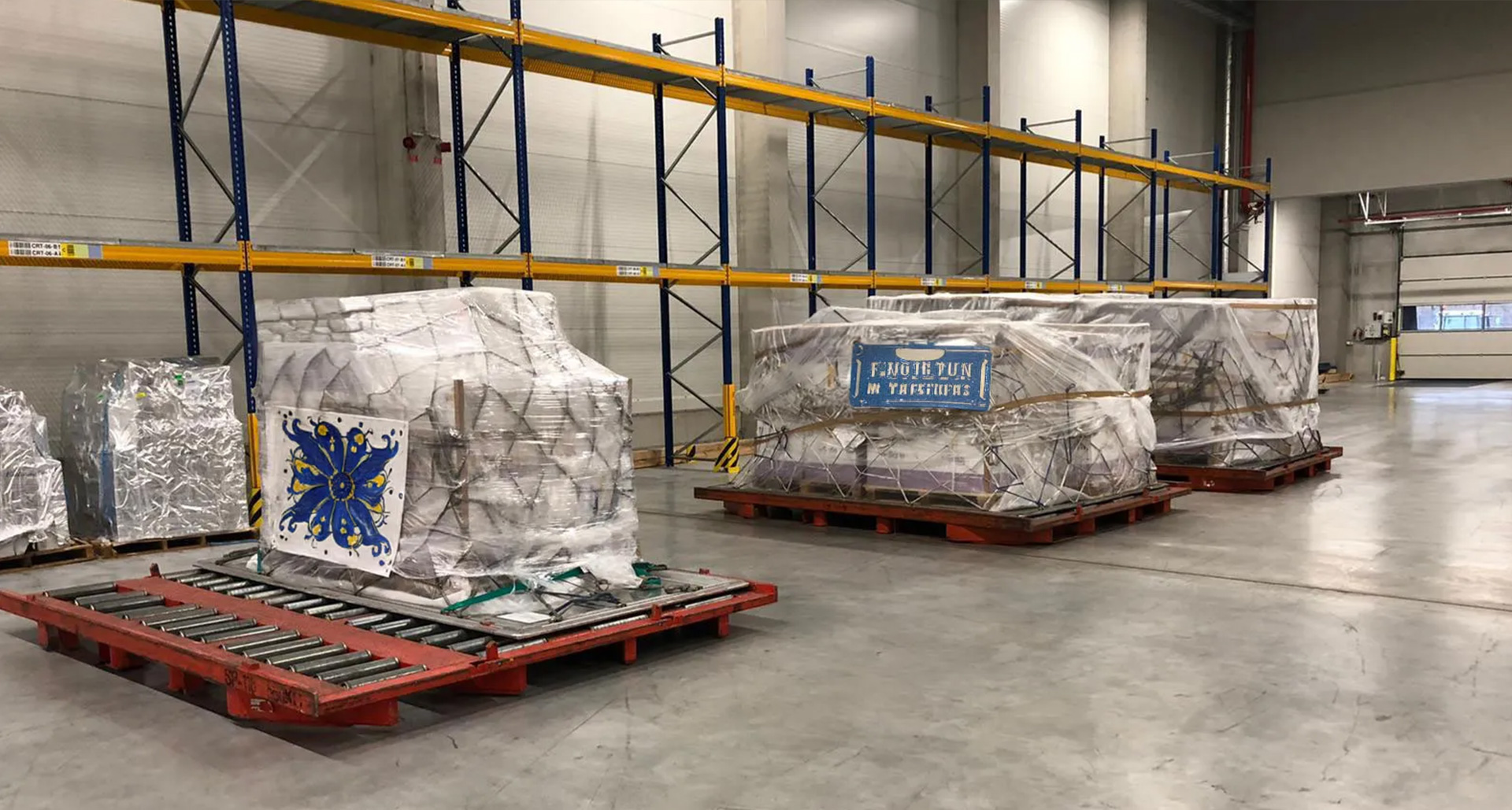
Example of a Code in Thematic Analysis
Quote | Code | Description |
---|---|---|
“if an engineer had to be called and they give us a paper with all the information, then we scan that and add it to the report before placing it on the repository so that all of it is in the same place.” | Data Matching Issues – Manual System | Code entails the issues with matching data when the shipment has arrived at the end of the supply chain. |
More Sample Codes
Code | Description |
---|---|
Established actions at workplace to mitigate temperature alerts | Code describes actions in a place defined by teams in the warehouse to act when there is an alert. |
Data Matching Issues – Manual System | Code entails the issues with matching data when the shipment has arrived at the end of the supply chain. |
Wastage of time with manual processes | Code represents the time lost in missing out on the collaborative solving of alerts. |
Failure of tech in monitoring | Code outlines the errors that might occur during the monitoring of temperature-sensitive goods. |
More Sample Themes
Theme | Description |
---|---|
IoT systems in place | Different systems have different working styles, helping understand how the system’s strengths or limitations affect team working styles. |
Teams in warehouse | Understanding teams and their dedicated roles in solving alerts identify where collaboration can be done. |
Alert Threshold workflows | Operating procedures are followed when there is a conditional excursion alert to solve the issue that might have been identified. |
Collaboration for quality control | Understand how teams work round the clock to make sure the quality is maintained. |
Limitations of the Study
-
Due to the COVID-19 pandemic, participants’ availability has decreased as their workload had increased.
- I was unable to visit more warehouses as i had intended to do earlier in my thesis.
-
Online interviews were conducted and not physical ones. As the interviews were not conducted in the natural surroundings of the participant, the details that the participant told is deemed to be true.
-
One of the participant’s first language was not English and sometimes had issues expressing themself during the interview.
-
Specific details such as names of software or customers are hidden due to confidentiality purposes.
Findings
Quote 1
“...depending on the product but it’s depending more on the regulatory or customer requirements than on the temperature range”
Quote 2
“…it’s still healthy to eat or healthy to consume a medical product. So I think for for everyone it’s very high priority”
-
The requirements of products change considerably from time to time – depending on what is stored in the warehouse, hence evolving storage practices of teams
- There is no standard IoT system in warehouses across locations, and it depends on the team’s best practices and previous experiences in handling alerts.
-
Humans consume Temperature-sensitive products in the end; therefore, there is a natural sense for priority to make sure all alerts are dealt on time
-
Depending on the time of day, users change that interact with the IoT system, hence not having a standard flow of practice.
-
The reliability of IoT systems is good but not optimal when workers have to solve the issue, which requires better collaboration practices.
My recommended implications for design
Define clear roles in the warehouse for alert threshold workflows
the future system could showcase the employee’s role and signify what action to take as part of the team.
Provide access to Alerts
usage of dedicated wearables(or a smartwatch application) could be explored for quick, precise commands (reducing delay in response time; not getting confused with regular email notifications)
Standardize the severity of Alerts
there are different allowed conditional ranges for storage requirements where the product quality is comprised. An indication of the severity of the alert could indicate how quickly the employee must react to it.
Conceptualize a system with predictive actions
based on knowledge-sharing and experience from shared locations, predictive actions could be shown as options for a more precise set of actions (figuring out the cause of an issue takes a lot of time)
Conclusion
1.
The interaction challenges faced in a warehouse are based on several factors such as the product’s requirements to act upon the alert, alert threshold workflows established in teams, limitations of IoT devices being used in a warehouse.
2.
IoT Systems help in successfully carrying out the condition monitoring tasks. Still, more research is needed for every team to identify their work practices and set up workflows to solve conditional alerts in warehouses.
3.
The quick and precise knowledge of the cause of the temperature alert is missing, which leads to delay in solving alerts. The system could recommend options to the user, rather than the teams having to figure every aspect by themselves.
Together with a mentor, we developed a solution that can be installed easily in any condition monitoring warehouse with IoT devices, enabling all operations and management related officials have a quick look and be alerted of errors that could occur during the handling, hence playing a huge role during the Covid-19 crisis.
This thesis lead to a
commercial solution for DHL
which is now live
in 20+ countries.
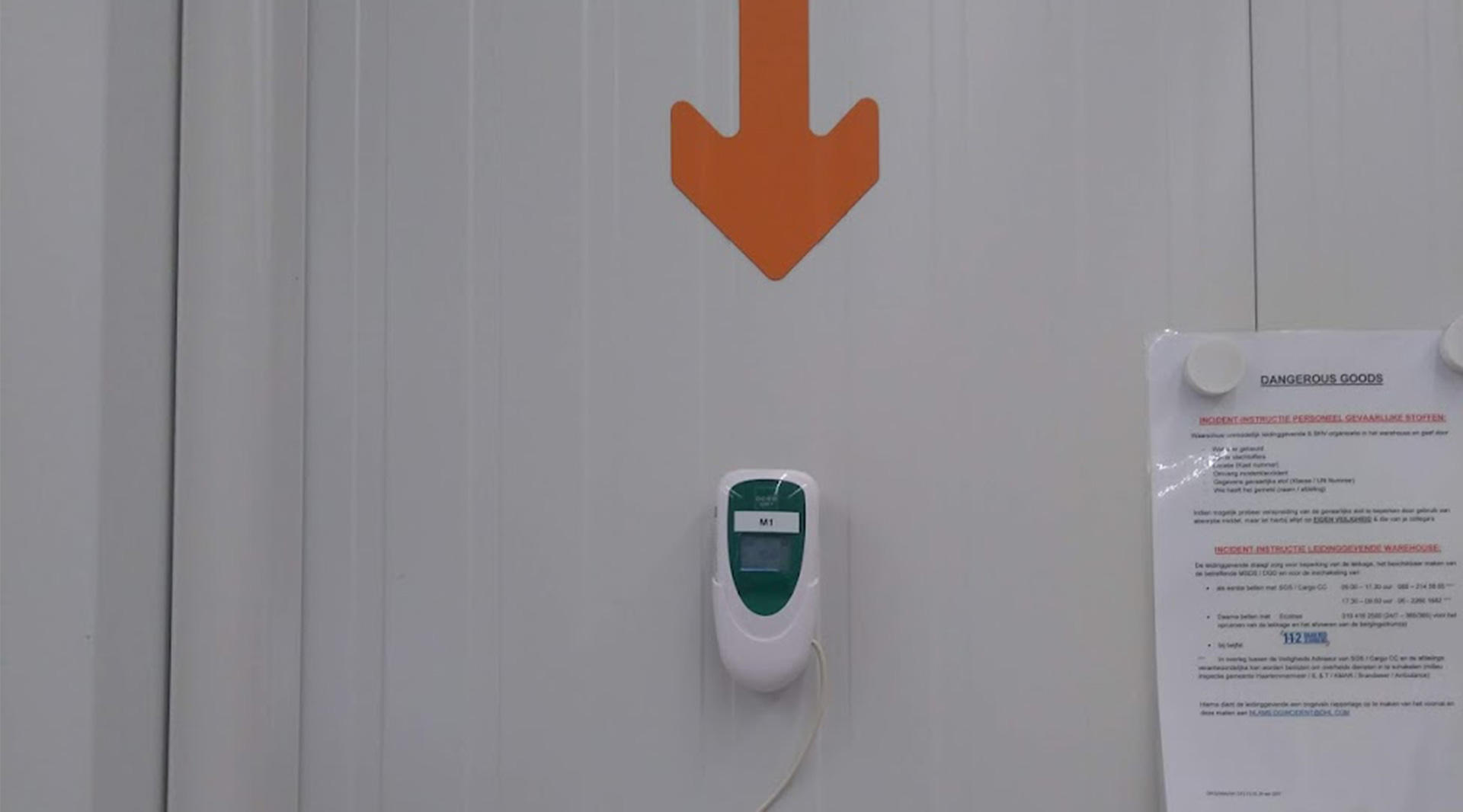
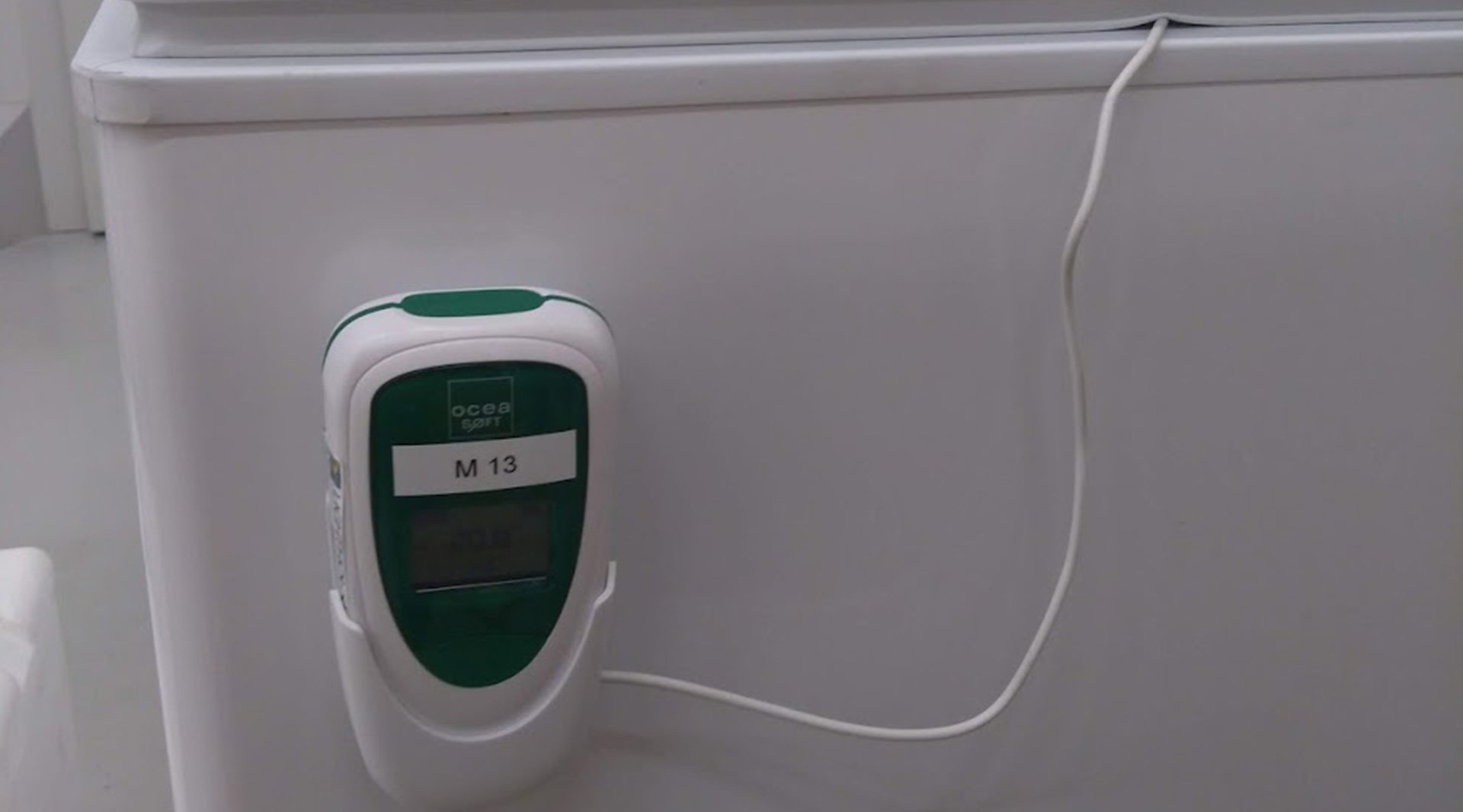
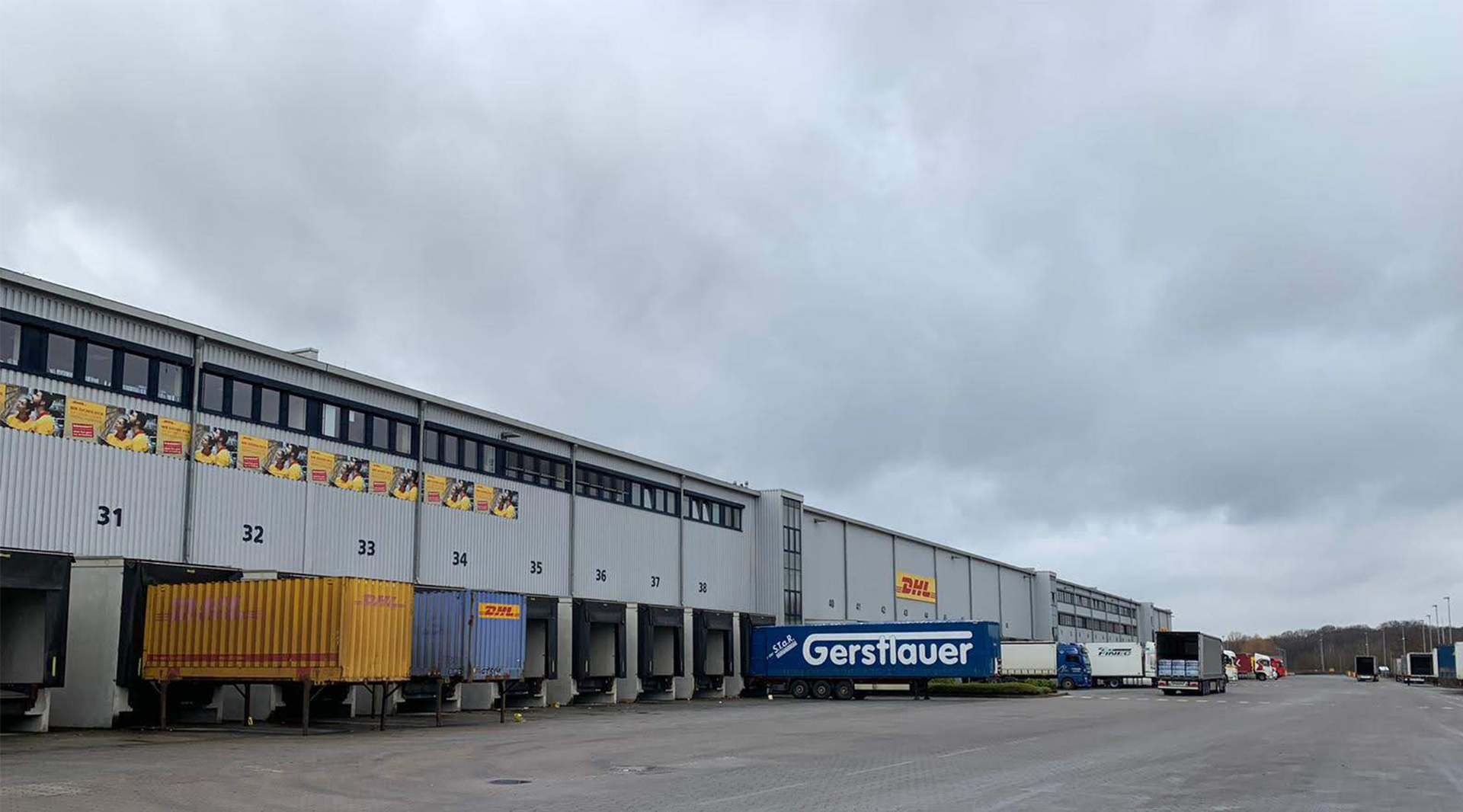
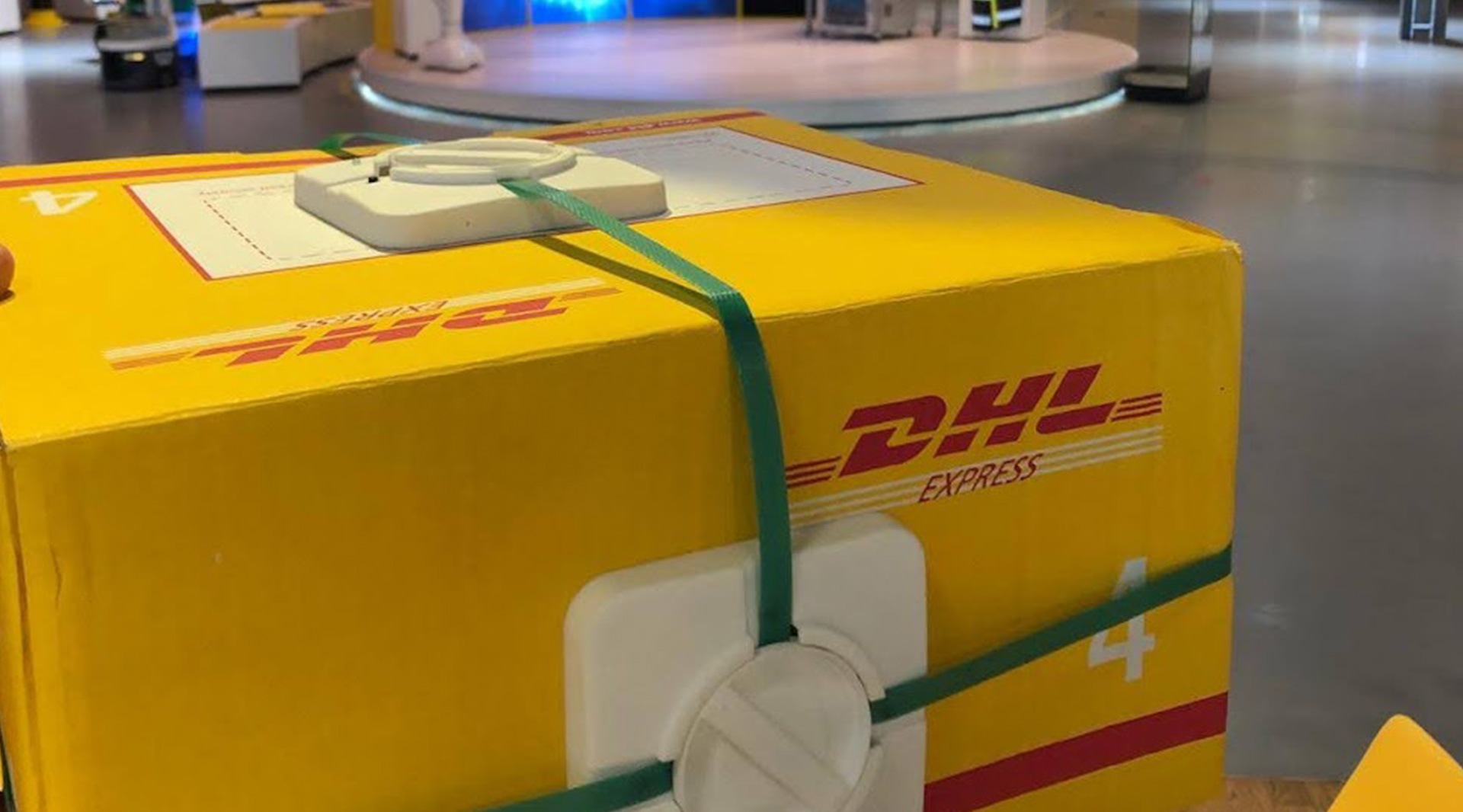
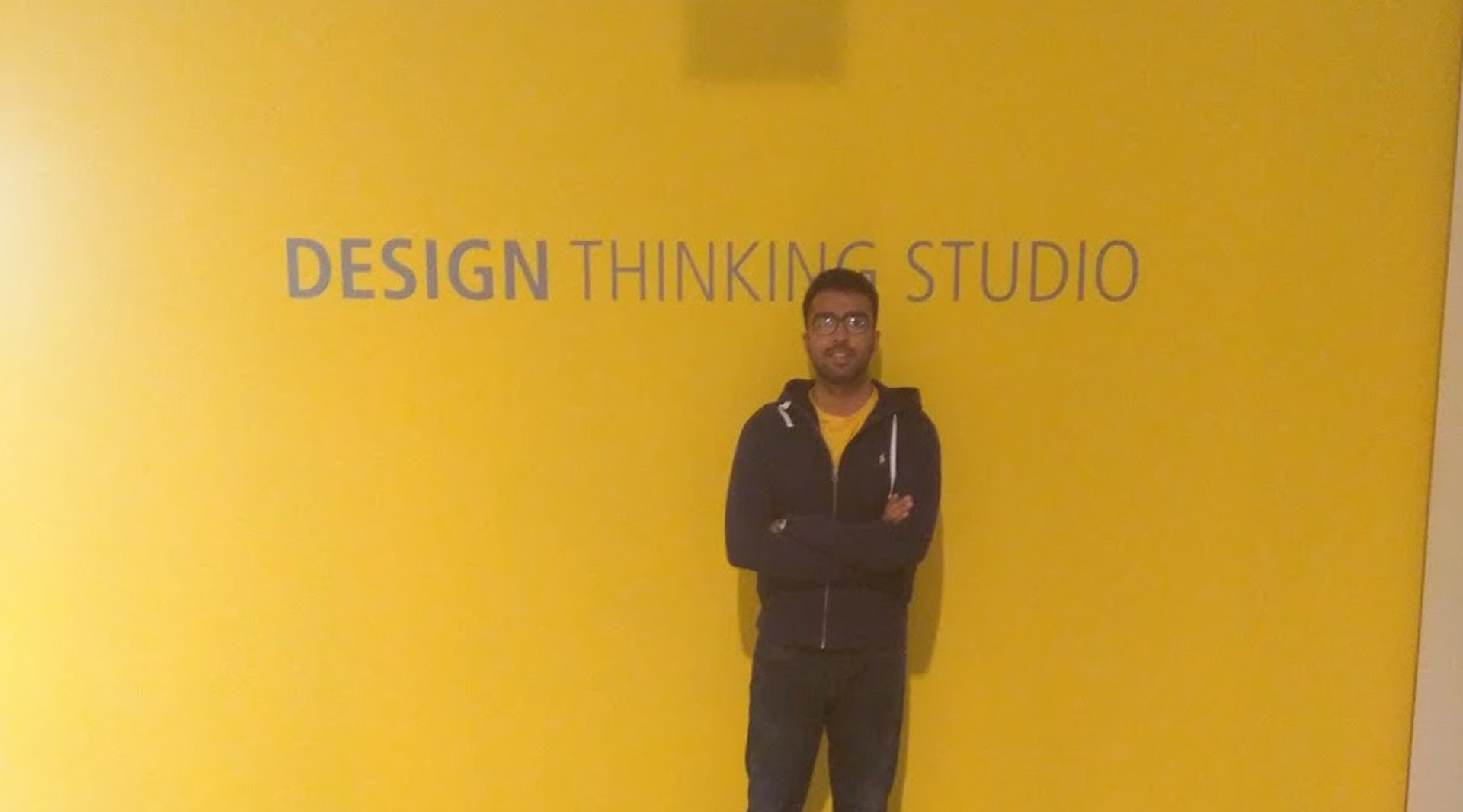
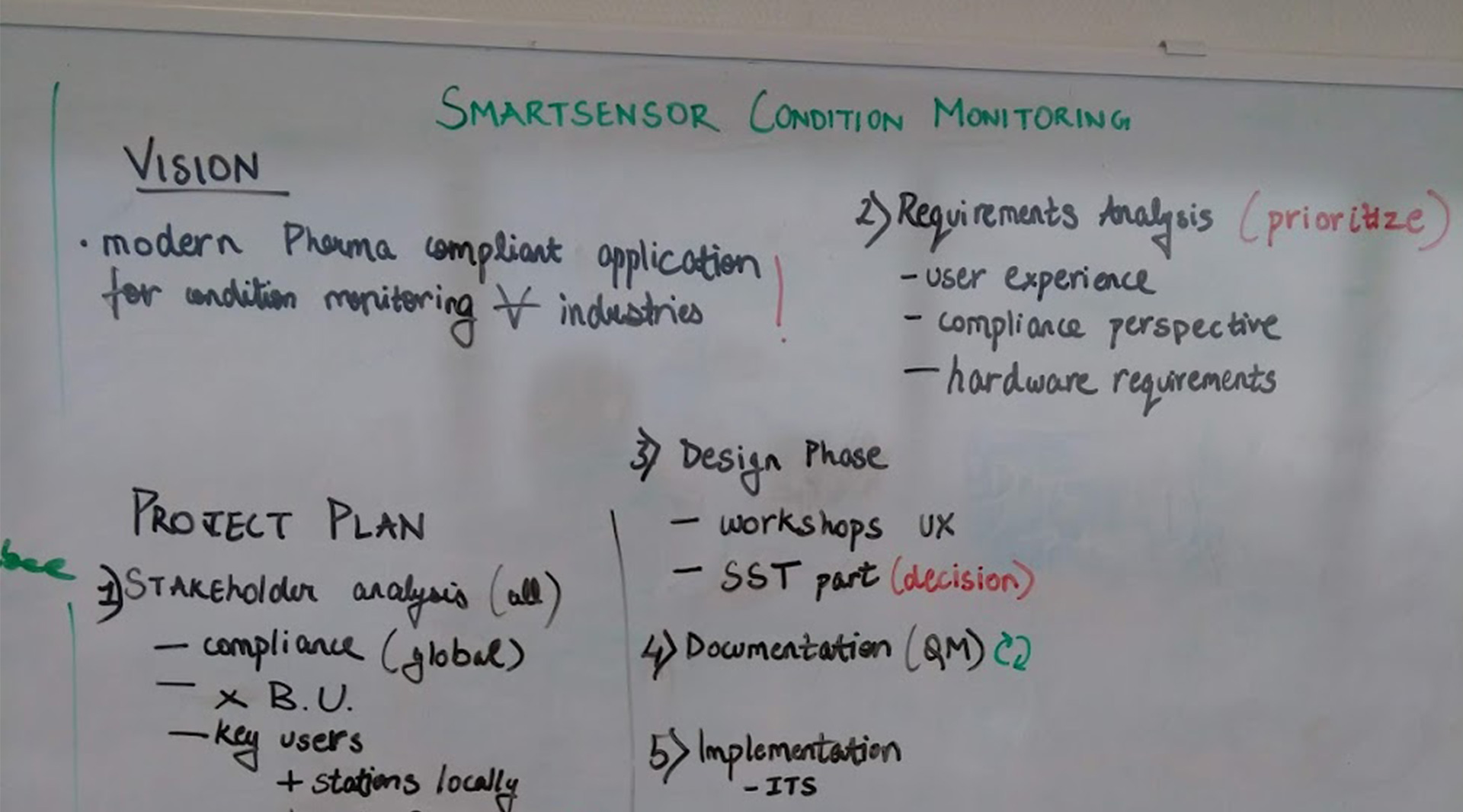